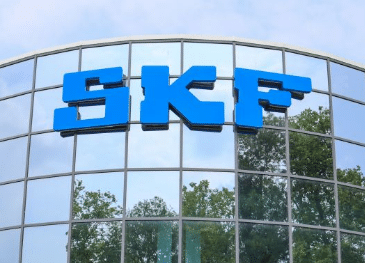
Introduction:
The textile industry is a cornerstone of modern society, providing us with the fabrics we wear and use in our daily lives. Within this industry, textile machinery plays a crucial role, and the reliability and performance of these machines largely depend on their components, including bearings. NSK and SKF, two renowned bearing manufacturers, have a strong presence in the textile machinery sector. In this comprehensive comparison, we will explore NSK bearings and SKF bearings for textile machinery applications, highlighting their unique features, performance, and significance in the industry.
Challenges in Textile Machinery Applications:
The textile industry presents unique challenges, including:
High Speeds: Textile machinery operates at high speeds to meet production demands, necessitating bearings capable of managing heat and friction.
Precision and Accuracy: To produce high-quality fabrics, textile machinery must maintain precision and accuracy in yarn feeding and fabric formation.
Continuous Operation: Textile machines often operate continuously, requiring bearings with an extended service life to minimize downtime and maintenance costs.
Contamination Resistance: Textile environments are prone to lint and dust, which can affect bearing performance and lifespan.
NSK Bearings for Textile Machinery Applications:
NSK is known for delivering high-performance bearings suitable for textile machinery applications. Key features and advantages include:
Advanced Material Technology: NSK employs advanced materials and coatings to enhance bearing durability, making them resistant to wear, corrosion, and contamination.
Precision Engineering: NSK’s precision engineering processes result in bearings with minimal dimensional variations and tight tolerances, critical for maintaining the precision and accuracy of textile machinery.
High-Speed Performance: NSK offers bearings optimized for high-speed textile machinery applications, ensuring quick and consistent fabric production.
Longevity: NSK bearings are engineered for reliability and durability, reducing downtime and maintenance costs for textile manufacturers.
Protection from Contaminants: NSK provides sealing and shielding options to protect bearings from lint, dust, and other contaminants prevalent in textile environments.
Customization: NSK offers customization options to tailor bearings for specific textile machinery applications, ensuring optimal performance.
SKF Bearings for Textile Machinery Applications:
SKF is also a prominent player in the textile industry, offering bearings designed for optimal performance in textile applications. Key features and advantages include:
Advanced Materials: SKF utilizes high-quality materials and coatings to enhance bearing durability, wear resistance, and corrosion resistance, essential for textile machinery applications.
Precision Engineering: SKF’s precision engineering processes result in bearings with minimal dimensional variations and tight tolerances, ensuring reliable and accurate textile production.
High-Speed Performance: SKF offers bearings optimized for high-speed textile machinery applications, ensuring efficient and consistent fabric production.
Longevity: SKF bearings are designed for reliability and durability, reducing maintenance costs and downtime for textile manufacturers.
Protection from Contaminants: SKF provides sealing and shielding solutions to protect bearings from lint, dust, and other contaminants prevalent in textile environments.
Customization: SKF offers customization options to ensure that bearings meet the specific requirements of different textile machinery applications, delivering optimal performance.
Conclusion:
In the textile industry, where high speeds, precision, longevity, and reliability are paramount, both NSK and SKF have established themselves as trusted providers of high-performance bearings.
The choice between NSK and SKF bearings for textile machinery applications should consider specific requirements such as high-speed performance, precision, longevity, contamination resistance, and customization needs. By carefully evaluating these factors, textile professionals can make informed decisions that enhance the efficiency, reliability, and cost-effectiveness of fabric production, ensuring the consistent quality of textiles.